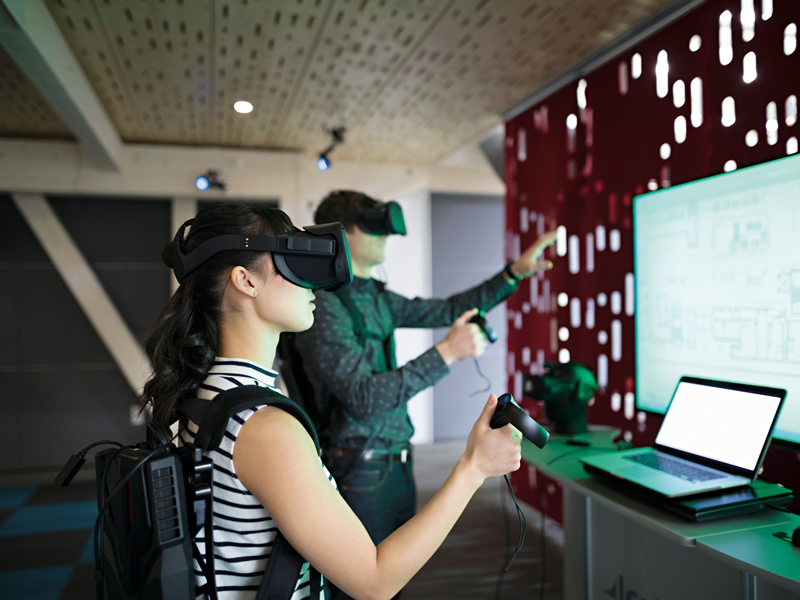
Progress often goes unnoticed. When we shop online, we don’t think about the automation, manufacturing and logistical challenges that have had to be overcome to enable next-day delivery. Equally, consumers are not forced to contemplate the industrial practicalities of moving towards renewable energy, electric cars and anti-counterfeit medicine.
Behind the scenes, though, industry is gripped by the transformative requirements of succeeding in a brave new world, and a very real test of intelligence is playing out for both humans and machines. Companies must thread the connections between the digital, physical and human elements of their business as they strive to meet the demands of new consumers, depleting global resources and humanity’s seemingly insatiable appetite for progress.
Each company will need to find its own path, but none should travel that path alone
European CEO spoke to Susana Gonzalez, President of Europe, the Middle East and Africa (EMEA) at Rockwell Automation, the world’s largest company solely dedicated to industrial automation and information, about the challenges and opportunities presented by the Fourth Industrial Revolution.
What does the current industrial environment look like?
It is an exciting time to be part of the industrial sector. New possibilities in the form of smart cities, personalised manufacturing, renewable energy and the electrification of cars are on the brink of changing the world.
These consumer trends have translated into changes in the way manufacturers produce goods: in order to bring products to market faster, reduce costs, make products more competitive and adapt to global trends in a safe and secure way, many companies are embarking on a digital, connected enterprise journey.
To achieve this, manufacturers face challenges including identifying a starting point, finding the right talent and setting up tools to analyse and interpret information.
How can companies overcome these challenges?
As a technology company and a manufacturer, we have been through our own digital transformation. In many ways, it’s an ongoing process, so we have a lot of experience overcoming challenges and incorporating our own technology into our manufacturing footprint.
Each company will need to find its own path, but none should travel that path alone. For instance, we work with partners such as Cisco Systems, Microsoft and PTC to bring other aspects of our transformation to life for our customers.
But for many in the EMEA region, the toughest challenges continue to be internal. Through our recent global customer research, we found that the top concern companies have during a digital transformation is building a team that can drive the necessary changes. Developing a digitalisation strategy and funding upgrades also ranked towards the top of the list.
So it’s not about buying technology, but rather about people and partnerships?
We believe digitalisation brings people, processes and technology together. Much of the technology is already available, so employees remain the most important asset an enterprise has, as people are the key to unlocking the potential of technology. Investing in the workforce through a lifelong learning approach is an important way to tackle the skills challenges facing industry at present.
Have you faced any challenges being a female leader in a male-dominated industry?
In 2017, Eurostat found that 83 percent of scientists and engineers within high and medium-high-technology manufacturing were male. This puts a lot of pressure on women like me to be a role model, to share career trajectories and encourage women to follow their career dreams. I feel strongly about the need to foster a culture of inclusion that goes beyond gender diversity. Countless studies have proven that diverse teams make better decisions, drive higher levels of innovation and achieve better results.
What is the most important consideration for a company navigating a digital transformation?
I would say two things: first, there must be a commitment at the leadership level. Driving a digital transformation without leadership from the top is difficult, as it requires process changes, equipment modernisation and investment, as well as collaboration between information and operation technology teams.
Second, you don’t have to do it alone. Bringing in the right vendors, service providers and systems integrators can be the key to moving from concept to implementation.